NON-DESTRUCTIVE AND SURFACE ENHANCEMENT INFORMATION
NON DESTRUCTIVE TESTING DESCRIPTIONS (MAG PARTICLE AND PENETRANT INSPECTION)
Magnetic particle Inspection (MPI) is a non-destructive testing
(NDT) process for detecting surface and shallow subsurface discontinuities in ferromagnetic materials
such as iron
,
nickel
,
cobalt
, and some of their alloys. The process puts a magnetic field into the part. The piece can be magnetized by direct or indirect magnetization. Direct magnetization occurs when the electric current is passed through the test object and a magnetic field is formed in the material. Indirect magnetization occurs when no electric current is passed through the test object, but a magnetic field is applied from an outside source. The magnetic lines of force are perpendicular to the direction of the electric current, which may be either alternating current
(AC) or some form of direct current
(DC) (rectified AC).

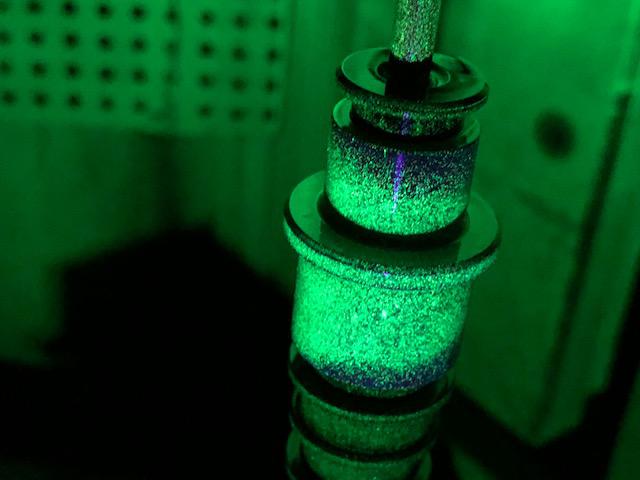
The presence of a surface or subsurface discontinuity in the material allows the magnetic flux
to leak, since air cannot support as much magnetic field per unit volume as metals.
To identify a leak, ferrous particles, either dry or in a wet suspension, are applied to a part. These are attracted to an area of flux leakage and form what is known as an indication, which is evaluated to determine its nature, cause, and course of action if any.
To identify a leak, ferrous particles, either dry or in a wet suspension, are applied to a part. These are attracted to an area of flux leakage and form what is known as an indication, which is evaluated to determine its nature, cause, and course of action if any.
Fluorescent Penetrant Inspection (FPI) operations use a dye much more sensitive to smaller flaws than penetrants used in other DPI procedures. This is because of the nature of the fluorescent
penetrant that is applied. With its brilliant yellow glow caused by its reaction with ultraviolet radiation, FPI dye sharply contrasts with the dark background. A vivid reference to even minute flaws is easily observed by a skilled inspector.
Because of its sensitivity to such small defects, FPI is ideal for most metals which tend to have small, tight pores and smooth surfaces. Defects can vary but are typically tiny cracks caused by processes used to shape and form the metal. It is not unusual for a part to be inspected several times before it is finished (an inspection often follows each significant forming operation).
Selection of inspection type is, of course, largely based on the material in question. FPI is a nondestructive inspection process which means that the part is not in any way damaged by the test process. Thus, it is of great importance that a dye and process are selected that ensure the part is not subjected to anything that may cause damage or staining.
Because of its sensitivity to such small defects, FPI is ideal for most metals which tend to have small, tight pores and smooth surfaces. Defects can vary but are typically tiny cracks caused by processes used to shape and form the metal. It is not unusual for a part to be inspected several times before it is finished (an inspection often follows each significant forming operation).
Selection of inspection type is, of course, largely based on the material in question. FPI is a nondestructive inspection process which means that the part is not in any way damaged by the test process. Thus, it is of great importance that a dye and process are selected that ensure the part is not subjected to anything that may cause damage or staining.
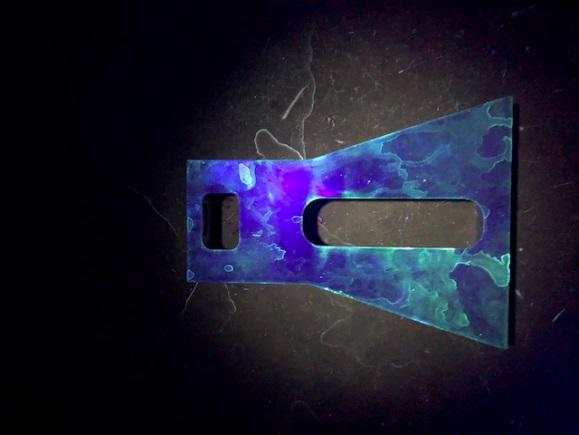
To compliment our Heat Treating and Electroplating operation, we offer:
- Magnetic particle inspection
- Dye penetrant inspection
- Nital etch inspection
- Salt spray testing
- One high humidity test chamber
Non-destructive Testing:
- Magnetic particle
- Dye penetrant
- Nital etch
- Salt spray
- High humidity
In-house laboratory for testing of Case Depth, White Layer, Micro Hardness, Microstructure Analysis, and Hardness.
Surface Enhancement:
- Blast cleaning
- Painting
- Shot Peening
- Solid film lubricant
Shot Peening a surface spreads it plastically, causing changes in the mechanical properties of the surface. Its main application is to avoid the propagation of micro-cracks from a surface. Such cracks do not propagate in a material that is under a compressive stress; shot peening can create such a stress in the surface.
Shot peening is often called for in aircraft repairs to relieve tensile stresses built up in the grinding process and replace them with beneficial compressive stresses. Depending on the part geometry, part material, shot material, shot quality, shot intensity, and shot coverage, shot peening can increase fatigue life up to 1000%.
Shot peening is often called for in aircraft repairs to relieve tensile stresses built up in the grinding process and replace them with beneficial compressive stresses. Depending on the part geometry, part material, shot material, shot quality, shot intensity, and shot coverage, shot peening can increase fatigue life up to 1000%.
Glass bead peening is an effective way of increasing the fatigue properties of metal parts and resistance to stress corrosion cracking. Glass beads are very hard and lightweight thus producing a high magnitude layer of residual compressive stress while leaving a smooth surface finish. This is beneficial in many metal fatigue applications where surface finish is the concern.
Glass beads are a non-ferrous media and are readily used to peen non-ferrous metals such as aluminum and stainless steel. Glass beads are available in smaller media sizes than steel peening media making them useful on delicate parts with intricate geometry.
Glass beads are a non-ferrous media and are readily used to peen non-ferrous metals such as aluminum and stainless steel. Glass beads are available in smaller media sizes than steel peening media making them useful on delicate parts with intricate geometry.
ISO 9001 with AS9100D Registered
Nadcap Accredited AS7108.
For more information contact 801-972-5590